

#Electro magnet manual#
Innovation and development of new assembly methodologies were required to eliminate manual assembly of “closed structures.” Leading the aircraft industry, we at Boeing invented, developed and implemented semi-automated systems using electromagnets for “closed structures” such as fuselage barrel sections and wing box assemblies. All assembly operations had to be performed manually.
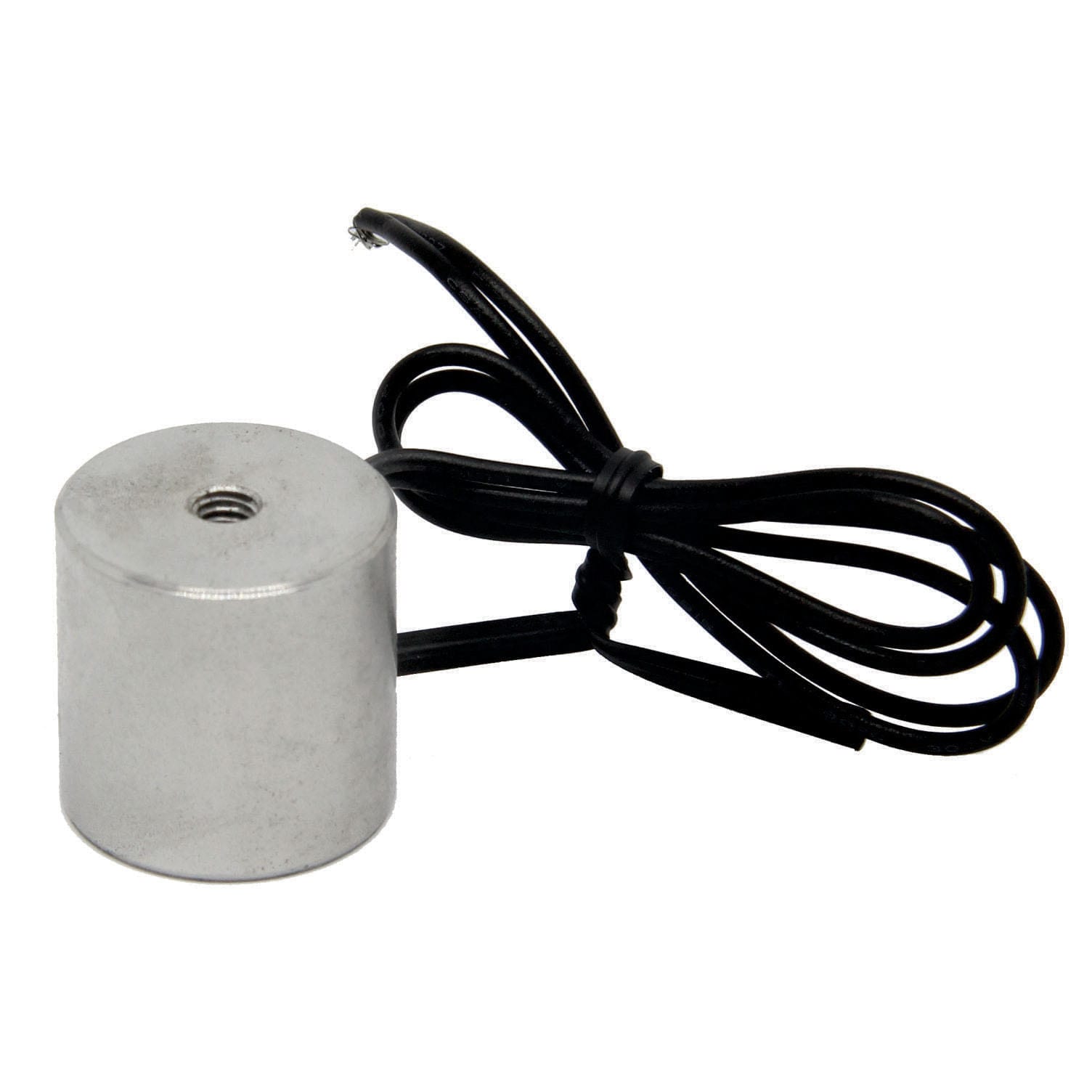
However, if assembly of “closed structures” like fuselage barrels and wing boxes is required, these C-frame machines cannot be used. The fuselage is built in five assembly steps (single, super/mega panels, half shells, barrels and complete fuselage) and wing is built in four major assembly steps (single panels, spars and ribs, spar/rib grid, and upper and lower panels assembly-creating the box), and integrating wing center box with the left and right wing box. Because of the force flow around the sub-assembly, only certain types and sizes of structures can be assembled with these machines-for example, single, super and mega fuselage and wing panels, allowing access to both sides of the structure (open structure).įigures 2 and 3 show fuselage and wing type of structures and assembly levels required to build step-by-step a complete fuselage and wing. Machine part clamping requires two bushings (one on each side of the sub-assembly), and active and re-active clamping forces are carried around the part by the C-frame machine structure (see Figure 1 “C-Frame Clamping”). A variety of C-frame and D-frame machines and systems are available today to perform “one-up-assembly” for rivets or fastener installation, significantly improving process efficiency and reducing time and cost of structural assembly. Chips enter the gap, necessitating part disassembly and cleaning, which leads to a two-step assembly process.ĭecades ago, aircraft manufacturers motivated suppliers to develop a machine, which could accomplish “one-up-assembly” by clamping pre-assembled parts at the drilling location to avoid gaps between parts, and to eliminate part disassembly and the cleaning process. As can be seen, the drilling is performed in-between two Clecos, and as soon as the first part is drilled, parts spring back-the drill bit continuously applying drilling force to the second part-resulting in a gap between parts. Figure 1 “Cleco Clamping” illustrates the behavior of parts during the manual assembly. The manual process is very time consuming.
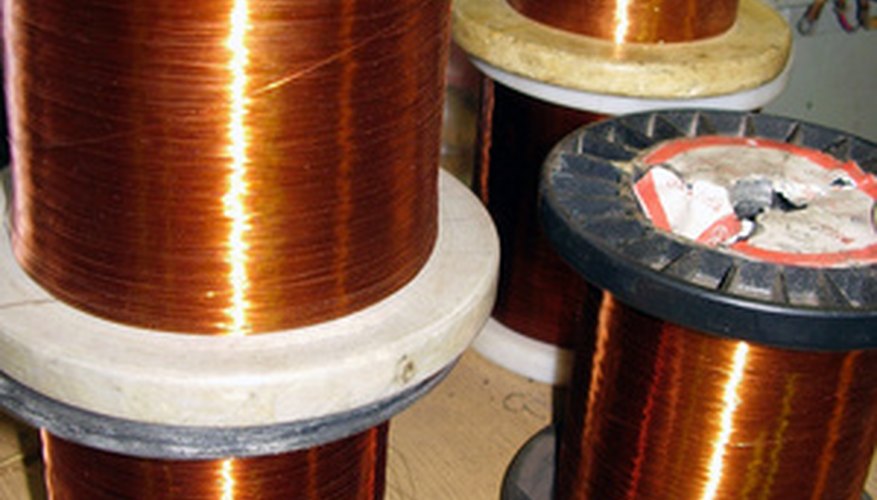
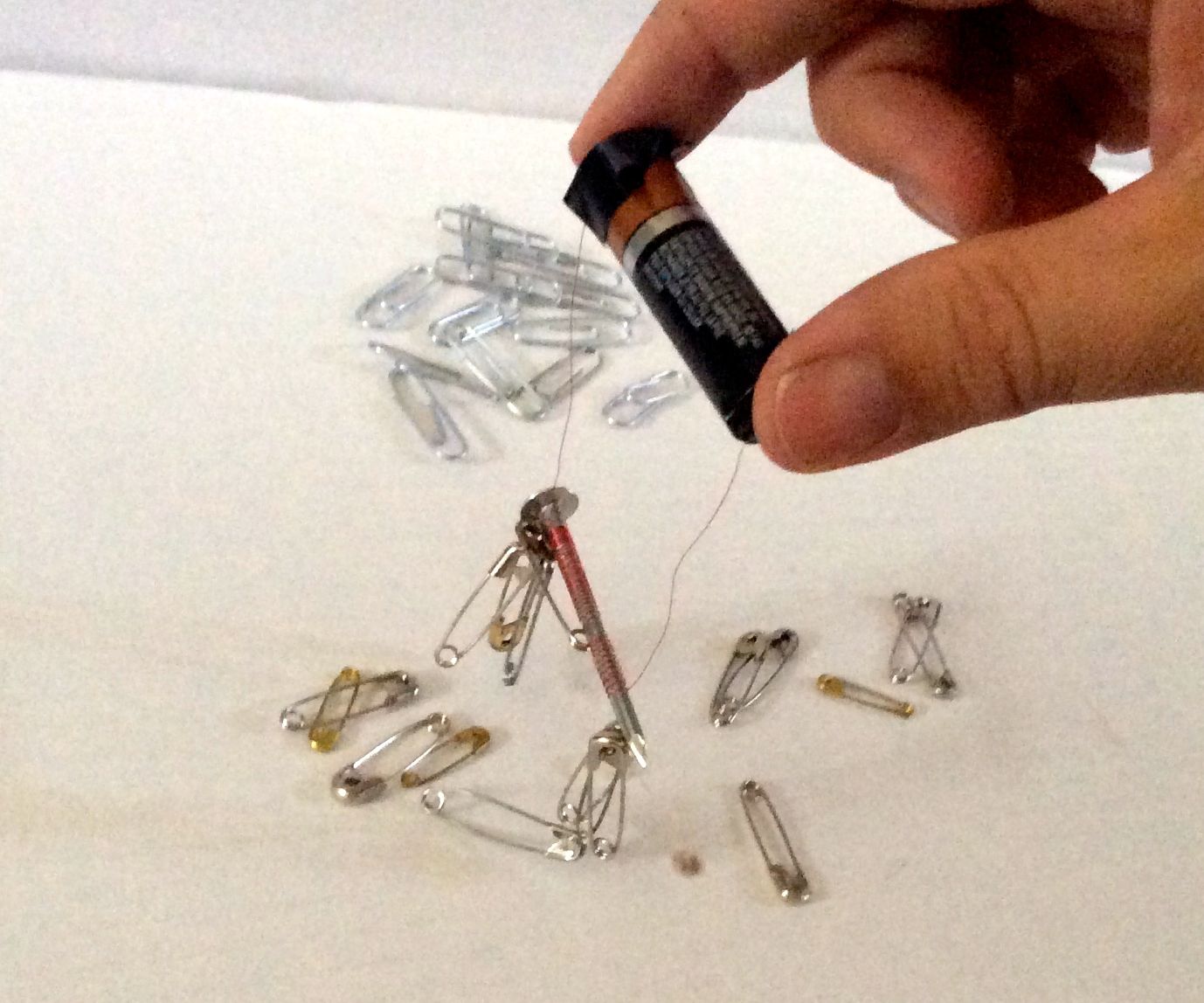
Basic processes involved in manual assembly include: What assembly technology is being used depends on type of components, structural configuration, available equipment, investment and the level of innovation created during the development of advanced assembly techniques and systems.Ĭonventional assembly processes use manual tasks to join parts to small sub-assemblies, and then integrate stepwise multiple sub-assemblies and panels to major components like fuselage and wing structures. Today’s aircraft assembly involves several methodologies and systems, ranging from conventional manual assembly to mechanized, semi-automated and fully automated systems. Within this paper, the design and equipment characteristics are described in some detail, and opportunities for advancing the part clamping methodology with emerging electropermanent magnets is described. Developing and integrating electromagnets into aircraft assembly systems was a major innovative step in improving assembly processes for manual and semi-automated operations.
